Geralmente o revestimento em pó pode ser considerado como um método ambientalmente favorecido da aplicação de um acabamento, particularmente no que diz respeito a evitar a utilização de tintas à base de solventes, evita o desperdício de excesso de pulverização, e qualquer pó não utilizado pode ser totalmente reciclado e utilizado novamente. Apesar de este processo ter sido concebido como um método de acabamento de metal, a tecnologia evoluiu de modo que agora é uma escolha comum para cerâmicas, plásticos e até mesmo madeira.
A pesquisa mostra que o revestimento em pó é o meio de revestimento de crescimento mais rápido e com as vantagens ambientais, juntamente com as suas excelentes propriedades de acabamento, é uma tendência que provavelmente continuará.
Tipos de revestimento em pó
Existem dois tipos principais de revestimentos em pó termofixos e termoplásticos;
Com variações termofixos, pois como o pó é aquecido, ele reage com os produtos químicos no polímero fazendo com que aumente o peso molecular; melhorando as propriedades de desempenho.
Os tipos de termoplásticos não mudam especificamente, nem tem quaisquer reações adicionais, eles simplesmente fluem para o revestimento final.
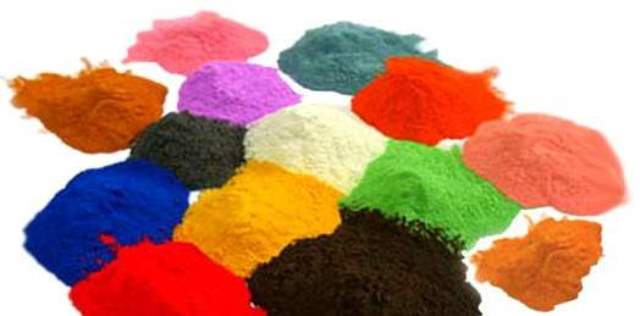
Tipo de revestimento em pó
Processo de revestimento em pó
Fase 1 – Pré-tratamento
Trata-se de preparar o componente ou parte, e como qualquer aplicação de pintura, a preparação é muito importante para alcançar o melhor acabamento possível.
É essencial remover óleos e lubrificantes e óxidos de metal e esta operação é realizada geralmente por uma variedade de métodos químicos e mecânicos, depende também do material, tamanho, e acabamento necessário.
Os vários estágios de pré-tratamentos químicos normalmente envolvem o uso de fosfatos ou cromatos em submersão ou por pulverização.
A partir de uma perspectiva ambiental, aqueles que oferecem preparações de fosfato são a opção preferida, pois os cromatos podem ser tóxicos para o meio ambiente.
Outro método de preparação é o jateamento e granalha, no qual o jateamento abrasivo é usado para dar textura à superfície e preparação para madeira, plástico ou vidro.
Carboneto de silício é adequado para moagem de metais, para o plástico são utilizados abrasivos de plástico que são sensíveis a substratos tais como o alumínio.
Fase 2 – A aplicação de pó
O método mais utilizado é a pulverização eletrostática por meio de uma pistola de pulverização.
O objeto é aterrado e uma pistola fornece uma carga elétrica positiva sobre o pó que é em seguida pulverizado e acelerado em direção ao componente pela carga eletrostática poderosa.
O componente é aquecido, fazendo com que o pó se funda formando uma película uniforme, e se arrefecendo para formar um revestimento duro. Por vezes, é necessário aquecer primeiro o metal e depois pulverizar o pó sobre o substrato quente. O pré-aquecimento pode ajudar a conseguir um acabamento mais uniforme, mas também pode criar outros problemas, que podem ser causados pelo excesso de pó.
O pó também pode ser aplicado usando especificamente discos eletrostáticos adaptados. Outro método, conhecido como o método de leito fluidificado, envolve o aquecimento do substrato e, em seguida, mergulhando-o em um leito aerado, cheio de pó.
O pó adere e derrete no objeto quente, com posterior aquecimento necessário para terminar a cura do revestimento. Este método é geralmente usado quando o revestimento for superior a 300 micros.
Revestimento em leito fluidificado eletrostático: a aplicação do leito fluidificado eletrostático utiliza as mesmas técnicas de fluidização mencionadas acima, mas com a profundidade pó muito menor na cama. A carga eletrostática ocorre no leito de modo que o pó seja carregado como o ar de fluidização elevando-o. Partículas carregadas de pó formam uma nuvem que é carregada por cima do leito fluido. Quando uma parte aterrada é passada através da nuvem carregada, as partículas serão atraídas para a sua superfície. As partes não são pré-aquecidas.
Revestimento eletrostático com escova magnética (EMB) é um método de revestimento para materiais planos, que se aplica em revestimento em pó com a técnica de rolo.
Fase 3 – Cura
Quando pós termofixos são expostos a elevados aumentos de temperatura, (normalmente através de um forno de cura por convecção ou infravermelhos), eles começam a derreter, fluir para fora e, em seguida reagem para formar um polímero de elevado peso molecular. Este processo de cura, chamado reticulação, exige certo grau de temperatura durante certo período de tempo a fim de alcançar a cura completa e estabelecer as propriedades dos filmes completos para o qual o material foi concebido.
Quais são as desvantagens do revestimento em pó?
– Revestimentos muito finos podem mostrar furos
– Mudanças de cor muito frequentes pode consumir muito mais tempo
– Cantos internos podem ter baixa espessura
– Pode ser complicado em cantos afiados
– Precisa de especialistas para manter a uniformidade de espessura
– Correspondência de cores e uniformidade pode ser mais difícil do que com tintas líquidas
Quais são as vantagens das tintas em pó?
– Ecologicamente correto – sem exigência de solventes
– Custo-benefício
– Os acabamentos são resistentes e flexíveis, tornando mais difícil lascar ou rachar
– Geralmente dá um revestimento 100% sólido
– Quase não produz resíduo
– Enorme gama de cores e acabamentos
– Oxidação livre
– Pode ser aplicado sobre uma vasta gama de espessuras
– Pode produzir revestimentos espessos, sem escorrer ou perder a firmeza
– Os efeitos especiais são facilmente realizados
– Rápido tempo de resposta
– Proteção contra desbotamento UV externo
– Retenção de cor excepcional
– Excelente capacidade de isolamento elétrico
– Resistente à maioria dos produtos químicos e solventes
Conclusões
Revestimento em pó; embora seja um sistema econômico, não só completa as qualidades desejadas estéticas do produto, mas também oferece uma excelente durabilidade e resistência a arranhões e corrosão química, mesmo nos ambientes mais adversos.
Ao utilizar este sistema, os pós são imediatamente prontos para utilização e não necessitam de mistura, o que elimina as variáveis em acabamento, reduz o tempo de processamento e resulta em propriedades da película de qualidade superior.
- Talvez você queira ler matérias:
- Por data de publicação
- Por ordem alfabética